Les usines s’arrêtent régulièrement pour des entretiens mineurs et majeurs (inspections, réparations…). Sans arrêts de maintenance programmés, les équipements peuvent tomber en panne, entraînant des dommages humains ou environnementaux, en plus de considérablement impacter la chaîne industrielle. Voici 4 conseils pour planifier l’arrêt temporaire d’une usine en limitant son impact.
Industrie – 4 conseils pour réussir la planification des arrêts temporaires d’usine
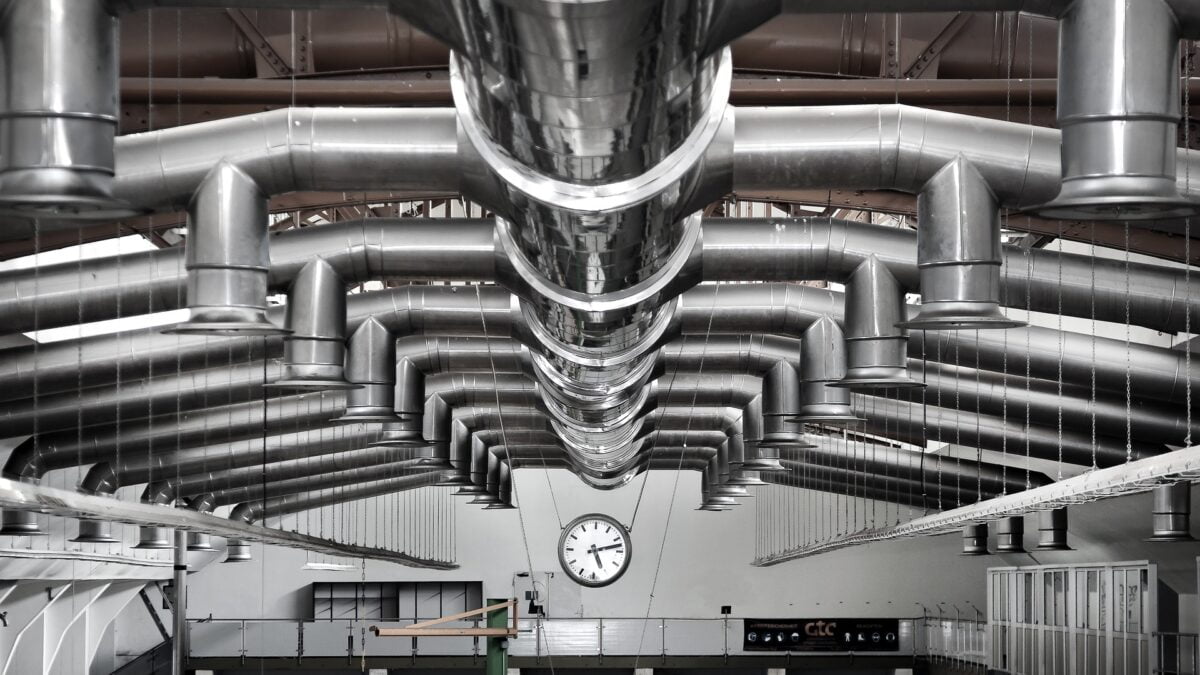
Mieux vaut prévenir que guérir
A l’usure, certains composants d’une usine peuvent devenir obsolètes. Même il est possible de poursuivre les opérations malgré cette détérioration, des arrêts sont forcément nécessaires à un moment donné pour assurer l’inspection, la réparation de ces composants.
En cas de maintenance, les employés comme les sous-traitants sont mobilisés et doivent participer à la préparation et à l'exécution de cet arrêt. En plus d’être soudains et non productifs, les arrêts non planifiés sont nettement plus coûteux que ceux prévus à l’avance, car généralement beaucoup plus graves. Le risque est en effet bien plus élevé si une usine subit un incident de sécurité (blessures voire décès ou dommages environnementaux…) ou de processus parce que des problèmes n’ont pas été décelés à temps. L’intégrité structurelle et les performances et la fiabilité en sont très rapidement impactés.
Suivre un calendrier strict de maintenance préventive représente beaucoup d’avantages. Il est possible d’effectuer une maintenance proactive et prévenir l’obsolescence des matériaux ainsi que les coûts associés à leur réparation.
Les avantages de l'arrêt planifié d'une usine
Les arrêts planifiés permettent de garantir que l'équipement de l'usine est dans un état optimal, en plus d’en garantir sa gestion. Les produits sont ainsi de meilleure qualité ; les rejets, les défauts, les processus correctifs ou de reprise sont diminués, et la répétabilité augmentée. Outre l’efficience opérationnelle, le secteur des achats peut aussi anticiper de son côté l’ensemble des investissements à venir, et passer des commandes en amont pour maintenir avec précision son inventaire.
Le personnel peut également identifier rapidement les problèmes potentiels et programmer dès lors une maintenance corrective avec un impact minimal sur la production. Cette anticipation engendre une amélioration nette de la sécurité, une forte diminution des risques encourus par les employés et les sous-traitants, et par conséquent, des temps d'arrêt imprévus prévus pour les réparations et les commandes d'urgence coûteuses.
Comment mettre en place une stratégie d’anticipation des arrêts temporaires au sein des usines ? Voici 4 conseils pour limiter leur impact :
Chercher les causes profondes des défaillances
Trouver la défaillance d'équipements critiques peut provoquer de longs retards dans le démarrage des arrêts d'urgence, et causer des pertes de production importante. L'analyse des données des processus permet de trouver la cause profonde des problèmes de démarrage ou autre dans l'usine. Certaines solutions rendent possible, grâce à la collecte des données, la génération de rapports en temps réel et personnalisés, essentiels pour avoir une vue d’ensemble et d’identifier la cause profonde de certains problèmes de défaillance.
Toujours analyser les données des actifs régulièrement
Pour mener à bien un arrêt, l’analyse des données des technologies de maintenance prédictive avant la date de l'arrêt est fondamentale, car elle identifie les défauts des actifs, leur gravité et leurs causes profondes. Il faut donc bien s’assurer d’avoir accès à ces données et qu’elles soient à jour, car elles sont essentielles pour déterminer la nécessité d'une maintenance, de réparations immédiates et de la programmation de l’arrêt de l'usine.
Des solutions de réalité numérique combinant logiciels, capteurs et technologies autonomes existent pour s’assurer de la bonne remontée et de la qualité des données des matériaux, en plus de déceler leurs défaillances potentielles. Les équipes peuvent surveiller ces constantes en ligne en temps réel grâce aux capteurs identifiant avec précision les défaillances avant même qu'elles ne se produisent. Cela permet au personnel de maintenance de programmer un arrêt et de se préparer en avance à une intervention, et ainsi prolonger la durée de vie des actifs.
S’assurer de la sécurité de l’usine avant, pendant, et après l’arrêt temporaire
Les arrêts planifiés avec des périodes de non-production, tout comme le maintien de la sécurité dans l'usine pendant l'arrêt sont essentiels pour s’assurer la sécurité des opérations de bout en bout. De nombreuses procédures non routinières sont en effet effectuées pendant les arrêts, et conduisent parfois à des situations inhabituelles et inattendues qui peuvent déstabiliser les agents de maintenance.
Disposer d’un module d’assistance de gestion de sécurité permet d’identifier et de contrôler toutes les activités, situations et matériaux dangereux afin de protéger le personnel et l'environnement. Il est important que ce module prenne en compte les réglementations en matière de santé, de sécurité et d'environnement (HSE), afin de s’assurer de la conformité des processus tout au long de l’arrêt temporaire.
Coordonner les arrêts temporaires à la gestion des actifs
La gestion des actifs de l'entreprise est précieuse pour l’augmentation de leur rentabilité, mais également pour la diminution des temps d'arrêt et l’amélioration de la sécurité. De nombreuses plateformes dédiée à l’asset management offrent des fonctionnalités essentielles pour la gestion des actifs et de leurs performances, mais également pour l’écosystème global des industries (gestion du travail, des matériaux, de la sécurité, des rapports, du budget, des investissements dans les actifs…).
Ces plateformes, dotées d’outils de planning et de gestion budgétaire, analysent les dépenses associées aux travaux de maintenance, et optimisent les investissements tout au long de la durée de vie de vos équipements. Des critères spécifiques à l’entreprise, comme la criticité ou le niveau de risque, sont utilisés pour hiérarchiser les actifs et permettent de créer de multiples scénarios et de décider ensuite de la meilleure stratégie à mettre en place. Ainsi, l’arrêt temporaire est anticipé, et les frais globaux des actifs diminués.
Les arrêts d'usine sont nécessaires aux usines, et ont besoin d’être supervisé par des logiciels de gestion stratégique des actifs, nécessaires pour la remontée et l’analyse des données de l’usine. Plus l’analyse est régulière, plus le temps de fonctionnement de l’usine est maximisé, sa sécurité renforcée et sa performance renforcée. Passer par ces 4 étapes résout déjà la plupart principaux problèmes auxquels les usines sont confrontées avant et pendant les arrêts.